Unknown Facts About Alcast Company
Unknown Facts About Alcast Company
Blog Article
The Only Guide to Alcast Company
Table of ContentsGetting The Alcast Company To WorkAll about Alcast CompanyWhat Does Alcast Company Do?Getting My Alcast Company To WorkAlcast Company for BeginnersAlcast Company Can Be Fun For Everyone
The subtle difference lies in the chemical material. Chemical Comparison of Cast Aluminum Alloys Silicon advertises castability by lowering the alloy's melting temperature level and boosting fluidity during spreading. It plays an important duty in permitting intricate mold and mildews to be filled up precisely. Furthermore, silicon adds to the alloy's toughness and use resistance, making it useful in applications where sturdiness is critical, such as auto parts and engine parts.It also improves the machinability of the alloy, making it less complicated to process into completed products. This way, iron contributes to the general workability of aluminum alloys. Copper raises electrical conductivity, making it advantageous in electric applications. It likewise improves corrosion resistance and contributes to the alloy's total toughness.
Manganese contributes to the toughness of light weight aluminum alloys and boosts workability (aluminum casting company). It is frequently used in wrought light weight aluminum products like sheets, extrusions, and profiles. The presence of manganese help in the alloy's formability and resistance to fracturing during manufacture procedures. Magnesium is a light-weight component that offers strength and impact resistance to light weight aluminum alloys.
Alcast Company Fundamentals Explained
It enables the manufacturing of light-weight elements with excellent mechanical buildings. Zinc boosts the castability of light weight aluminum alloys and aids control the solidification process during casting. It boosts the alloy's strength and firmness. It is frequently found in applications where complex forms and great details are required, such as ornamental castings and specific vehicle components.
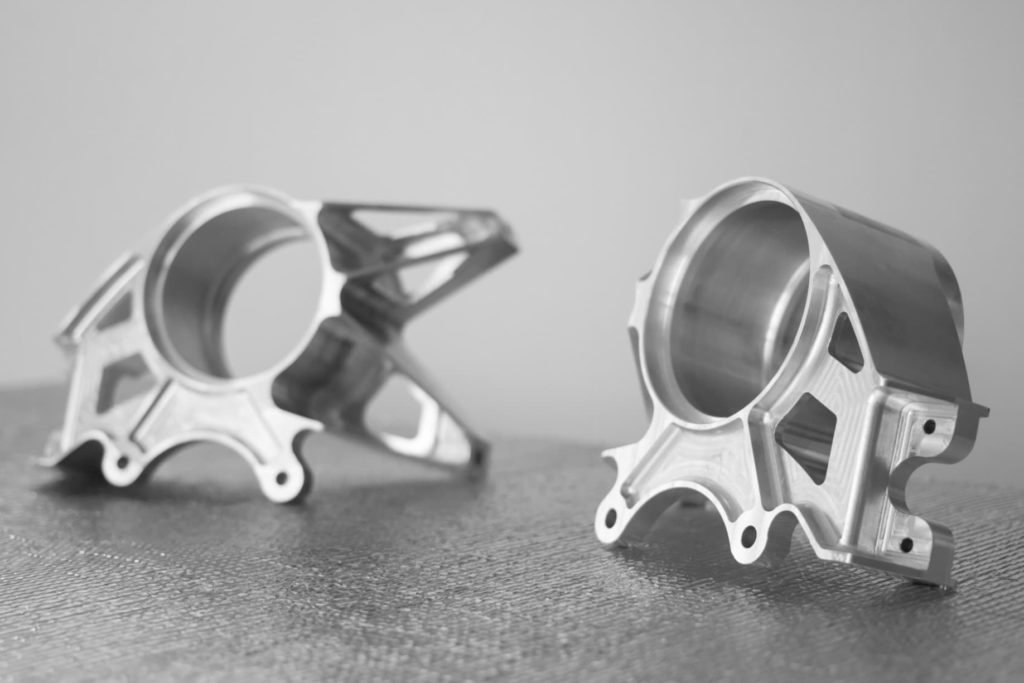
The key thermal conductivity, tensile toughness, yield stamina, and prolongation differ. Select ideal raw materials according to the performance of the target item generated. Amongst the above alloys, A356 has the highest possible thermal conductivity, and A380 and ADC12 have the cheapest. The tensile limitation is the contrary. A360 has the most effective yield stamina and the highest possible elongation rate.
Little Known Facts About Alcast Company.
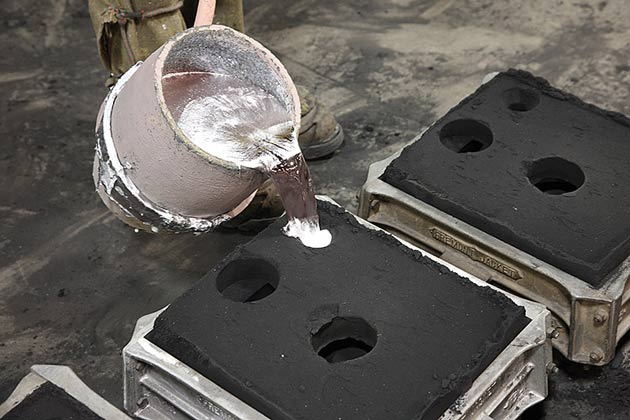
In precision spreading, 6063 is well-suited for applications where intricate geometries and top notch surface area finishes are critical. Instances include telecommunication rooms, where the alloy's premium formability enables smooth and visually pleasing layouts while keeping architectural stability. Similarly, in the Illumination Solutions market, precision-cast 6063 parts create classy and effective lighting fixtures that call for complex shapes and good thermal performance.
It leads to a finer surface area finish and far better rust resistance in A360. Additionally, the A360 displays remarkable elongation, making it optimal for facility and thin-walled parts. In accuracy casting applications, A360 is well-suited for markets such as Consumer Electronic Devices, Telecommunication, and Power Devices. Its improved fluidity permits for elaborate, high-precision elements like smart device housings and interaction tool housings.
Rumored Buzz on Alcast Company
Its unique buildings make A360 an important choice for accuracy spreading in these markets, boosting product toughness and high quality. Aluminum Castings. Light weight aluminum alloy 380, or A380, is an extensively utilized spreading alloy with several distinctive qualities.
In accuracy casting, aluminum 413 beams in the Customer Electronics and Power Devices sectors. It's typically used to craft detailed elements like smartphone housings, electronic camera bodies, and power tool housings. Its accuracy is impressive, with tight tolerances approximately 0.01 mm, guaranteeing remarkable item assembly. This alloy's superior rust resistance makes it a superb choice for outside applications, guaranteeing resilient, long lasting products in the discussed markets.
Alcast Company Fundamentals Explained
Once you have decided that the aluminum die casting process is ideal for your task, an essential next action is deciding on one of the most ideal alloy. The aluminum alloy you select will significantly influence both the casting process and the homes of the end product. Due to this, you need to make your decision thoroughly and take an informed method.
Figuring out the most ideal light weight aluminum alloy for your application will certainly suggest considering a large selection of features. The initial category addresses alloy attributes that affect the manufacturing procedure.
The Only Guide for Alcast Company
The alloy you select for die spreading straight influences numerous facets of the casting process, like how simple the alloy is to collaborate with and if it is vulnerable to casting defects. Warm breaking, also recognized as solidification fracturing, is a common die casting issue for light weight aluminum alloys that can lead to inner or surface-level splits or fractures.
Certain aluminum alloys are more vulnerable to hot fracturing than others, and your selection must consider this. It can damage both the actors and the die, so you ought to look for alloys with high anti-soldering properties.
Deterioration resistance, which is currently a significant characteristic of light weight aluminum, can differ considerably from alloy to alloy and is an important particular to consider relying on the environmental conditions your item will certainly be exposed to (Casting Foundry). Wear resistance is an additional building frequently looked for in light weight aluminum products and can differentiate some alloys
Report this page